RED OXIDE FLOORING
Red oxide, Black oxide and other color oxide flooring, unique to Kerala, is back in favour after falling from grace in the seventies. Many people from the nothern India and aboard exclaim at the richness and velvety gloss of a well-made oxide floor.
The best example of traditional red and black flooring is found in the 400-year-old Padmanabhapuram Palace in Thakkala.
However, with the arrival of the multitude of flooring materials such as Marble, Mosaic, Vitrified and other floor tiles, red/ black oxide fell out of popularity in the Seventies. It became more or less a poor man’s flooring. Now it is getting back its glory.
The technique of using coloured cement for flooring is found in other parts of India too, such as the Chettinad tiles. In Bangalore too, there were many old buildings made with oxide floors. Even carpet like patterns are embossed in the floor using different colours. The coloured flooring in the old houses in Goa also.
The old technique for the coloured floor used egg white, a lot like the fresco method. However, the quality of the oxide flooring, whatever the colour, depends a lot on the craftsmanship. Only an expert craftsman can lay a perfect floor without cracks and that does not develop patches with time. The process is laborious and requires keen attention.
The biggest attraction of the oxide flooring is its economic viability. Now various colours of oxide floors are available.
Follow these importantly for oxide floors
The day after doing the floor, cure the floor by sprinkling water every two to three hours for a whole day, to avoid a dry floor. The second day, a thin sheet of water should be stocked up to check if white patches appear on the floor. If they do, remove the water, rub them off with a cloth and again refill water, until no white patches are visible. Once the floor is laid, no one should walk on it for a minimum of four days, except for watering and waxing. Let the floor dry for a few days, clean it by wet and dry mopping and apply 400 grade sand paper in case smoothening and levelling is enquired. Red color wax should now be applied directly on the surface with a soft cloth.
As the wax dries, rub the surface with rice husk or coconut pith in circular fashion until the wax disappears. Keep the room closed for three days so that the floor absorbs the wax fully.
The finer points
- The water should be clean or treated, and definitely not the mineral-rich borewell water.
- White cement and high grade grey cements tend to set fast, hence not advisable. Sand should not have silt deposits on its surface, hence better to clean them before mixing.
- Quality of red oxide is important to ensure that wear and tear across the years does not expose the concrete beneath.
- For 1 part oxide, up to 3 parts grey cement gives dark red colour, while increasing cement quantity leads to light red shades.
- White cement too can be used to get different shades, but with utmost care.
- Cement and oxide should be first mixed in dry form, slowly adding water to get a consistent slurry-like Any lump formation in the mix will show up in the flooring. Trowelling to get an even surface is very important. While the minor undulations vanish during the hand polish, the major ones may remain.
- Oxide floors need to be done in one continuous stretch without break, often taking the whole day and night depending upon the area to be covered.
- Most materials deteriorate with age, but oxide floor is an exception. It shines more the longer it is used
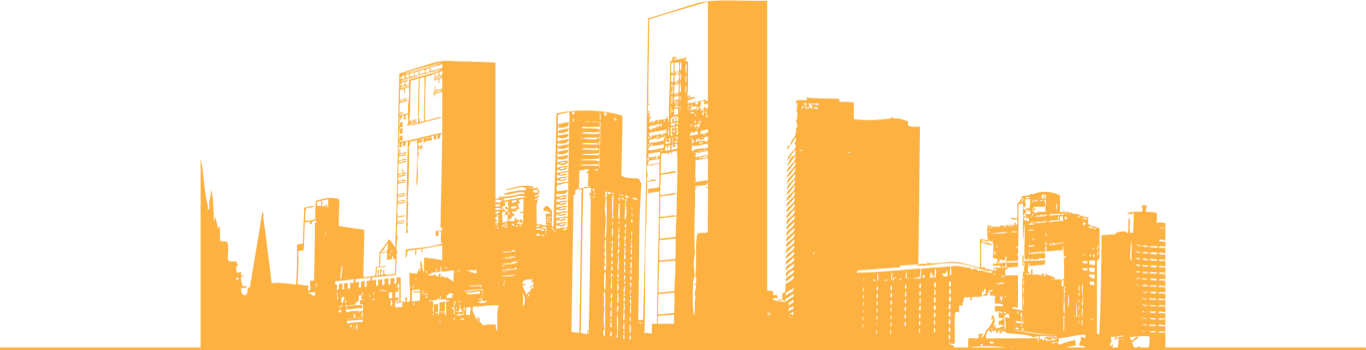